Hot Isostatic Pressing and Cold Isostatic Pressing Applications
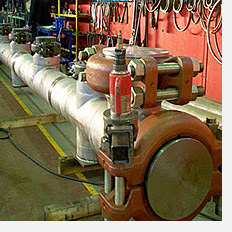
POWDER METALLURGY (PM)
Examples of Hot Isostatically Pressed PM
PM Offshore Oil and Gas Manifold
- Net shape on ID and OD surfaces
- Only machined on mating faces
- Welded into 40 ft assemblies
- Lighter in weight than comparable wrought components
PM Steam Chest
- The can at top shows complex inner detail
- The finished part at bottom is machined only on mating faces
- 12% Cr steel
Consolidation of metal powder
Processing of encapsulated metal powders by hot isostatic pressing consolidation has been used extensively since 1970. Major uses include billet preforms for forging/extrusion and near-net shape fabrication. The capsule material is usually stainless or carbon steel. After HIP, the container is removed by chemical etching or machining. Containers are fabricated to high quality standards to ensure a hermetic seal exists around powder or green compact. Ceramic and glass containers also are used for some applications.
Densification of cemented carbides
Hot isostatic pressing is a particularly effective process for removing internal flaws from sintered carbides. The carbide powder is cold pressed, dewaxed, sintered, and then subjected to HIP to eliminate residual porosity. It is widely accepted that for critical applications where increased strength is required, the HIP process greatly improves cemented carbides.
Sinter HIP
Conventional sintering produces parts containing some micro and macro porosity which is detrimental to strength and surface integrity when polished. Sinter hot isostatic pressing is used for vacuum or atmospheric sintering of parts with the introduction of gas to create moderate pressurization at the end of the sinter cycle.
Metal Injection Molding (MIM)
Metal injection molding components typically are greater than 95% of theoretical density as sintered. In some cases, typically for high-performance applications, the extra process of hot isostatic pressing is utilized to close any residual pores by the simultaneous application of heat and pressure, increasing part integrity, mechanical properties and corrosion resistance.
Examples of Hot Isostatic Pressed MIM Components:
Automotive
- Fuel injection valve components
- Turbocharger adjustment vanes
Firearms
- Firing pins
- Trigger
- Trigger guard
- Barrel
- Frame
Medical
- Surgical tools
- Dental implants
CASTING
Examples of Hot Isostatic Pressed Castings
Turbine engine components
- Structural castings
- Blades
- Vanes
Orthopedic implants
- Spine
- Hip
- Knee
- Shoulder
- Dental implants *also made using metal injection molding
- Surgical tools *also made using metal injection molding
Airframe Castings
- Aluminum and titanium alloys
- Replace machined slabs and fabrications
Commercial castings
- Turbocharger wheels
- Pump bodies
- Valve components
- Firearm parts
- Sterile enclosures
- High vacuum materials
Metal Additive Manufacturing / 3D Printing
A growing number of metals and metal composites are used for industrial grade additive manufacturing/3D printing. Stainless steel, aluminum, titanium, and cobalt are just a few. Hot isostatic pressing processing is expected to be utilized for high-performance applications and is currently specified on many aerospace components.
Examples of hot isostatic pressed metal additive manufacturing components:
Aerospace
- Fuel nozzle
- Turbine blades
- Combustor chamber
Medical
- Cranio-maxillofacial implant
- Acetabular cups
For more detailed information on how isostatic pressing can be used, visit our case studies section.
Case Studies